
PHARE: Prototype of a highly integrated skill-based embedded feeder (vibratory feeder)
The gradual digitization and automation of manufacturing processes and the networking of supply chains, in conjunction with concepts such as product-controlled manufacturing, require production systems that are highly integrated yet flexible in terms of production technology. Modularization of the production system is considered to be one solution approach to this challenge. The modularization of machining systems will be followed in the future by the modularization of material flow systems to enable even shorter time-to-market cycles and cost-effective implementation based on a fully networked network of interoperable automation components. In today's production systems, a variety of conveyor and feeding systems such as belt conveyors, roller and small conveyor belts are used as components for sorting, conveying and staging product components. Vibratory conveyor systems in particular have maintained their place in industry for many decades and represent an indispensable assembly for automated processes. Until now, these conveying and feeding systems have in the vast majority of cases not been integrated into the higher-level control processes and are often controlled manually via simple actuators such as potentiometers. With regard to their future role as networked and active components in a production system, the technical and economic requirements placed on these systems are increasing significantly, especially during commissioning, maintenance or troubleshooting. In the future, these requirements can no longer be met efficiently without intelligent control and networked communication of the components. As a result, customer demand for compact, energy-efficient and, above all, easy-to-integrate systems is increasing in a highly price-sensitive international market.
To tackle the above mentioned challenges, in PHARE the project partners Afag Automation and inIT are engaged with the project goal of a prototypical development of a highly integrated and skill-based embedded feeder (embedded vibratory feeder). This component is autonomous, i.e. independent of central MES systems and network connections, can be securely identified, configured and maintained via mobile devices and can itself be used as an active part of an IIoT manufacturing system.
For the prototypical realization of the highly integrated vibratory feeder, the power and control electronics - previously located outside the component compared to the conventional design - must be integrated into the component, including the necessary plug connections and operating elements. The resulting high integration density requires new solutions for the design and thermal management of the integrated electronics. For configuration and control integration, an OPC-UA and skill-based control concept of the DEVEKOS project is used. Secure identification and communication with the component for initialization purposes at locations in the field that are often difficult to access is realized via a commercially available mobile terminal via Bluetooth/WLAN. For deterministic and real-time communication, a solution based on Time Sensitive Networking (TSN) will be developed.
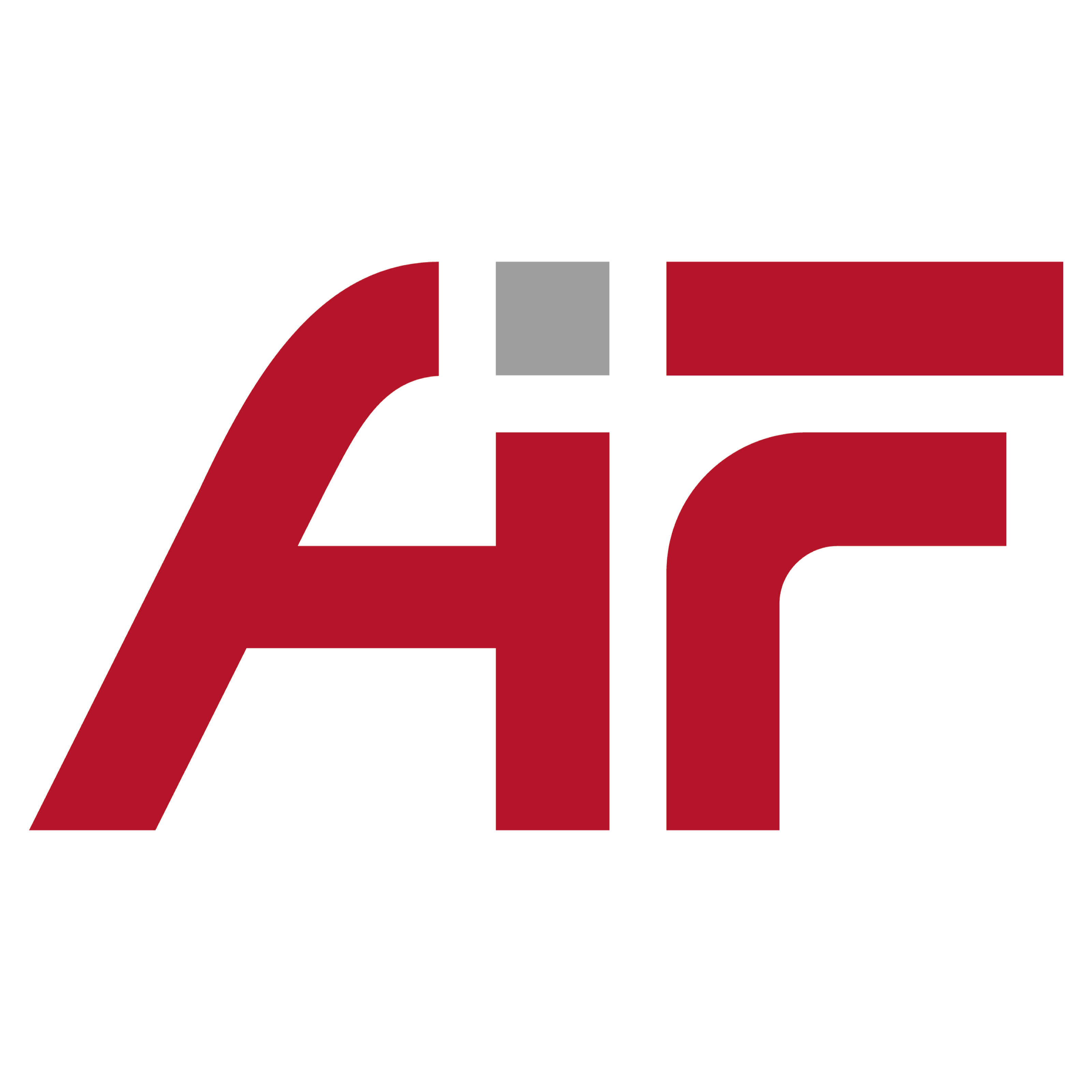